Aetna longer term care insurance coverage – Aetna long-term care insurance coverage provides a spread of choices to give protection to towards long run care wishes. This information supplies a transparent review of to be had plans, overlaying the entirety from advantages and prices to the enrollment procedure and coverage comparisons. Figuring out your choices is secret to meaking told selections about your monetary safety.
Navigating the complexities of long-term care insurance coverage may also be daunting, however this useful resource goals to simplify the method. We will discover the other protection choices, prices, and crucial main points that will help you make your only option on your explicit wishes.
Evaluation of Aetna Lengthy-Time period Care Insurance coverage
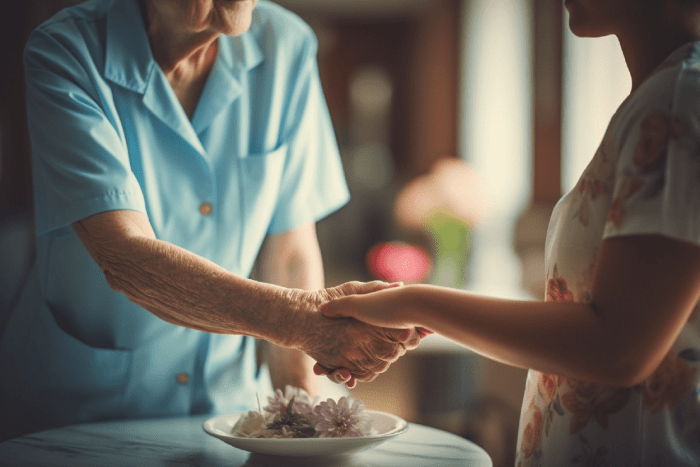
Aetna provides a spread of long-term care insurance coverage designed to lend a hand folks and households get ready for possible long run care wishes. Those plans supply protection for quite a lot of services and products, from professional nursing care to assisted residing, making sure monetary coverage all through a difficult duration. Figuring out the other protection choices, premiums, and deductibles is a very powerful for making told selections.
Protection Choices and Advantages
Aetna’s long-term care insurance coverage usually fall into other classes, every with various ranges of protection. Those plans can lend a hand offset the really extensive prices related to long-term care, together with professional nursing amenities, assisted residing, and residential well being care. The precise advantages and lines depends upon the selected plan and the person’s wishes. Aetna’s protection choices supply a very powerful monetary coverage all through classes of prolonged care.
Sorts of Protection
Aetna provides quite a lot of forms of long-term care insurance coverage, every with its personal set of advantages, premiums, and deductibles. Those plans range with regards to day by day or per month receive advantages quantities, and the period of protection they supply.
Plan Comparability Desk
Plan Identify | Protection Main points | Price Estimates |
---|---|---|
Aetna Lengthy-Time period Care Plan A | Supplies day by day advantages for knowledgeable nursing facility care, assisted residing, and residential well being care. Features a ready duration prior to advantages start. | Premiums get started from $XXX per thirty days, relying on age, well being standing, and receive advantages quantity. Deductibles might observe. |
Aetna Lengthy-Time period Care Plan B | Provides extra complete protection than Plan A, together with upper day by day receive advantages quantities for a much broader vary of care services and products. Might come with non-compulsory add-ons for explicit care wishes. | Premiums usually upper than Plan A, starting from $YYY to $ZZZ per thirty days, relying at the decided on protection stage. Deductibles might observe. |
Aetna Lengthy-Time period Care Plan C | Adapted for people with explicit wishes, corresponding to the ones requiring specialised care or the ones residing in positive geographic places. This plan might be offering extra flexibility with regards to protection choices. | Premiums are extremely variable in accordance with particular person wishes, with possible for a spread from $PPP to $QQQ per thirty days. Deductibles and out-of-pocket prices range. |
Notice: Price estimates are approximate and might range in accordance with particular person instances. Talk over with a monetary guide or Aetna consultant for customized knowledge.
Key Options and Advantages
- Receive advantages Quantity Flexibility: Aetna plans be offering quite a lot of day by day or per month receive advantages quantities, permitting folks to tailor protection to their monetary wishes and expected care bills. This permits folks to customise their protection to compare their anticipated care wishes and price range.
- Ready Sessions: Maximum plans have a ready duration prior to advantages start. This ready duration can range via plan and is a very powerful issue to believe when comparing protection choices.
- Caregiver Make stronger: Some plans might be offering fortify services and products to help caregivers, together with respite care or coaching systems, additional assuaging the weight of caregiving.
Advantages and Protection Main points
Aetna long-term care insurance coverage insurance policies supply monetary help for quite a lot of caregiving wishes all through prolonged classes of disability. Figuring out the particular advantages, protection sorts, and boundaries is a very powerful for making told selections. This segment main points the specifics of protection, serving to customers assess whether or not those insurance policies align with their particular person wishes.Aetna’s long-term care insurance coverage insurance policies usually duvet a spread of services and products, from professional nursing care to assisted residing and residential well being.
On the other hand, explicit advantages and boundaries range in accordance with the selected plan. Policyholders will have to moderately evaluation the coverage paperwork to grasp the total scope of protection.
Coated Care Products and services
Aetna long-term care insurance policies usually duvet professional nursing amenities, assisted residing amenities, and residential well being care services and products. The extent of care lined is incessantly outlined via the coverage’s explicit standards, which might come with the will for help with actions of day by day residing (ADLs) and/or instrumental actions of day by day residing (IADLs).
- Professional Nursing Amenities: Those amenities supply 24-hour scientific take care of folks requiring in depth scientific supervision and rehabilitation. Protection incessantly relies on the person’s want for knowledgeable nursing services and products, corresponding to wound care, bodily remedy, and medicine control.
- Assisted Residing Amenities: Those amenities supply a supportive surroundings for many who require help with day by day duties however don’t necessitate the extent of professional hospital therapy present in nursing properties. Protection might come with lend a hand with bathing, dressing, and meal preparation.
- House Well being Care: This provider delivers scientific and private care within the convenience of the insured’s house. Products and services would possibly come with professional nursing, bodily remedy, occupational remedy, and scientific social paintings, contingent at the coverage’s explicit phrases.
Obstacles and Exclusions
Now not all care services and products are universally lined. Insurance policies incessantly have boundaries or exclusions in regards to the forms of care, the period of protection, and the particular instances through which advantages are payable. Those boundaries will have to be totally tested when making an allowance for a coverage.
- Pre-Current Prerequisites: Some insurance policies will have exclusions or boundaries for pre-existing prerequisites. Which means positive well being problems provide prior to the coverage is bought is probably not lined or will have limited protection.
- Period of Care: Insurance policies usually specify a most receive advantages duration. This limitation signifies that the coverage would possibly not duvet care past a definite time-frame, although the will persists.
- Sorts of Care Now not Coated: Positive forms of care, corresponding to custodial care (which specializes in private care quite than scientific wishes), is probably not lined underneath the coverage. That is very true for positive plans interested by professional care.
Protection Eventualities
- Situation 1 (Protection): A policyholder calls for professional nursing care after a stroke. The coverage covers the prices of professional nursing facility take care of the period Artikeld within the coverage, so long as the care meets the coverage’s standards.
- Situation 2 (No Protection): A policyholder wishes help with day by day duties corresponding to bathing and dressing, however does no longer require professional hospital therapy. If the coverage’s standards for protection don’t come with custodial care, the prices related to this kind of care is probably not lined.
Comparability of Plan Choices
Plan Choice | Professional Nursing | Assisted Residing | House Well being | Most Receive advantages Length |
---|---|---|---|---|
Plan A | Sure (6 months) | No | Sure (restricted) | 24 months |
Plan B | Sure (limitless) | Sure (365 days) | Sure (limitless) | 36 months |
Plan C | Sure (6 months) | Sure (6 months) | Sure (6 months) | 365 days |
Notice: This desk is for illustrative functions handiest and does no longer constitute all imaginable Aetna long-term care plan choices. Explicit protection main points will have to be verified with Aetna immediately.
Price and Top rate Data
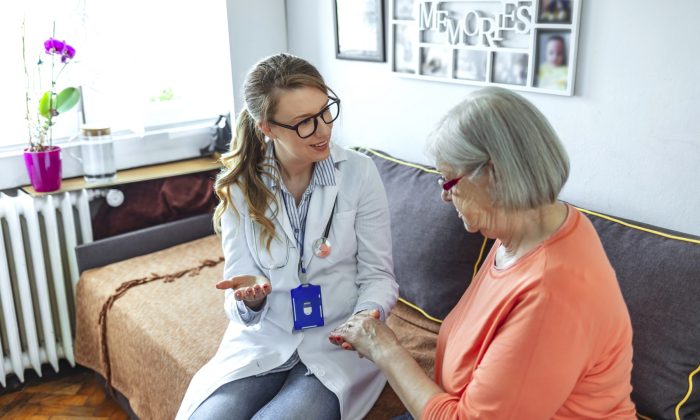
Aetna long-term care insurance coverage premiums are a significant component within the decision-making procedure for potential policyholders. Figuring out the price construction, together with premiums, deductibles, and co-pays, is a very powerful for comparing the monetary implications of various plans and protection ranges. This segment supplies an in depth review of those prices, highlighting possible diversifications in accordance with age and well being standing.Premiums for long-term care insurance coverage are usually calculated in accordance with a number of components.
Those components come with the specified protection quantity, the insured’s age and well being, and the particular advantages integrated within the plan. Figuring out those parts is important to as it should be assess the long-term monetary dedication.
Top rate Construction Breakdown
Premiums for long-term care insurance coverage insurance policies usually constitute the periodic bills made via the policyholder to take care of protection. The precise top class quantity relies on quite a lot of components, together with the coverage’s advantages and the policyholder’s age and well being. Insurance policies with upper protection quantities and broader advantages incessantly have upper premiums.
Top rate Permutations via Protection Stage
Other coverage choices be offering various ranges of protection, influencing top class prices. A coverage offering the next day by day receive advantages quantity or an extended duration of protection will usually have the next top class. Policyholders will have to moderately weigh the specified stage of protection towards the related price.
Top rate Permutations via Age
Age is a number one determinant of premiums. More youthful folks usually pay decrease premiums in comparison to older folks, as the danger of desiring long-term care is decrease at more youthful ages. Premiums building up because the policyholder’s age rises, reflecting the expanding probability of requiring long-term care services and products. This can be a elementary idea in insurance coverage pricing.
Top rate Permutations via Well being Standing
Aetna, like different insurers, might modify premiums in accordance with the policyholder’s well being standing. People with pre-existing well being prerequisites or the ones with the next chance of desiring long-term care might face upper premiums. This chance evaluate is very important to the insurance coverage trade and immediately affects pricing methods.
Instance Top rate Desk
Age | Protection Quantity (Day-to-day Receive advantages) | Estimated Annual Top rate |
---|---|---|
65 | $200 | $2,500 |
65 | $300 | $3,000 |
70 | $200 | $3,000 |
70 | $300 | $4,000 |
Notice: Those are illustrative examples and exact premiums might range considerably relying on particular person instances. This desk supplies a basic concept of possible price levels. The real top class will probably be made up our minds via the particular coverage decided on and the person’s well being evaluate.
Eligibility and Enrollment Procedure
Aetna long-term care insurance coverage insurance policies have explicit eligibility standards and enrollment procedures. Figuring out those facets is a very powerful for potential policyholders to resolve in the event that they qualify and the way to navigate the appliance procedure. The method usually comes to offering well being knowledge and demonstrating monetary wishes.Eligibility for long-term care insurance coverage is incessantly in accordance with components corresponding to age, well being standing, and fiscal instances.
The precise necessities range relying at the selected coverage and plan. Figuring out the stairs fascinated by making use of for and enrolling in a coverage is very important for a clean transition into protection. Pre-existing prerequisites might also impact eligibility and protection.
Eligibility Standards
Aetna insurance policies usually believe components like age, well being standing, and fiscal want. Candidates is also required to fulfill minimal age thresholds, relying at the coverage. Well being tests are incessantly carried out to judge a person’s present well being standing and chance of desiring long-term care. Monetary components, corresponding to source of revenue and property, might also play a job in figuring out eligibility.
Utility and Enrollment Procedure
Making use of for and enrolling in an Aetna long-term care insurance plans usually comes to a number of steps. A potential policyholder will have to moderately evaluation the coverage main points and necessities prior to beginning the appliance procedure.
- Accumulate important paperwork: Candidates wish to gather and get ready the desired paperwork, corresponding to evidence of source of revenue, well being data, and id. This preliminary step guarantees the appliance procedure proceeds easily and successfully.
- Entire the appliance shape: The appliance shape incorporates questions on private knowledge, well being historical past, and fiscal standing. Correct and entire knowledge is important for the insurance coverage corporate to evaluate eligibility and supply an acceptable coverage.
- Put up the appliance: The finished software and supporting paperwork will have to be submitted throughout the designated channels, incessantly on-line or via mail. Correct submission is very important for processing the appliance successfully.
- Underwriting and evaluation: The insurance coverage corporate’s underwriting division critiques the appliance, well being knowledge, and fiscal main points. This procedure evaluates the applicant’s chance profile and determines eligibility for the coverage.
- Coverage issuance: If the appliance is authorized, the insurance coverage corporate problems a coverage record outlining the phrases, prerequisites, and protection main points. This record is a legally binding settlement that defines the tasks of each the policyholder and the insurer.
- Top rate fee: The policyholder should make top class bills as scheduled to take care of lively protection. This ongoing legal responsibility is important for the coverage to stay in impact.
Pre-Current Situation Obstacles
Aetna’s long-term care insurance coverage insurance policies will have boundaries or exclusions associated with pre-existing prerequisites. Those boundaries usually contain ready classes or exclusions for explicit prerequisites. Candidates will have to moderately evaluation the coverage paperwork to grasp the particular provisions referring to pre-existing prerequisites. Aetna’s coverage language referring to pre-existing prerequisites might range relying at the explicit coverage and plan. Figuring out those boundaries is a very powerful prior to making use of.
As an example, some insurance policies would possibly have a ready duration of 6 months or extra for prerequisites that manifest prior to the coverage’s efficient date. Policyholders will have to seek the advice of the coverage paperwork for explicit main points.
Coverage Comparisons and Choices: Aetna Lengthy Time period Care Insurance coverage
Evaluating Aetna’s long-term care insurance coverage with the ones of alternative suppliers is a very powerful for told decision-making. Figuring out the diversities in protection, advantages, and pricing is very important to choosing a plan that perfect meets particular person wishes and fiscal instances. This comparability highlights key variations and offers examples of competitor plans.An intensive analysis of quite a lot of long-term care insurance coverage choices is important.
This comprises no longer handiest Aetna’s plans but in addition the ones presented via primary competition. The function is to offer a transparent image of the marketplace panorama and help folks in making well-informed possible choices about their long-term care insurance coverage.
Protection and Receive advantages Permutations
Other insurance coverage corporations be offering various ranges of protection and advantages. Elements like day by day receive advantages quantities, most receive advantages classes, and lined services and products can range considerably. Aetna’s insurance policies might duvet a spread of services and products, together with professional nursing care, assisted residing, and residential well being aide services and products, with various day by day receive advantages quantities and most protection intervals. Competitor plans might emphasize explicit facets of care or be offering extra complete protection.
Pricing and Top rate Comparisons
Premiums for long-term care insurance coverage are influenced via a large number of components, together with age, well being standing, and selected protection stage. Aetna’s premiums might range relying at the decided on coverage and particular person traits. Evaluating Aetna’s pricing with competitor plans is vital to evaluate affordability. Elements just like the period of protection, the quantity of day by day advantages, and the particular services and products lined considerably affect premiums.
Examples of Competitor Plans
A number of primary insurance coverage corporations be offering long-term care insurance coverage choices related to Aetna’s. As an example, Humana provides a spread of plans with various ranges of protection and premiums. Different competition, corresponding to Mutual of Omaha, additionally supply related plans. The collection of a plan relies on particular person wishes and personal tastes.
Comparative Research Desk
Characteristic | Aetna | Humana | Mutual of Omaha |
---|---|---|---|
Day-to-day Receive advantages Quantity (USD) | $200-$500 | $150-$400 | $250-$600 |
Most Receive advantages Length (days) | 1,000-3,000 | 1,500-3,650 | 1,800-4,000 |
Coated Products and services | Professional nursing, assisted residing, house well being | Professional nursing, assisted residing, reminiscence care | Professional nursing, assisted residing, hospice care |
Top rate (Instance, age 65) | $500-$1,500 yearly | $400-$1,200 yearly | $450-$1,400 yearly |
Notice: Premiums and receive advantages quantities are examples and might range in accordance with particular person instances. At all times visit a monetary guide for customized suggestions.
Claims Procedure and Buyer Provider
The claims procedure for long-term care insurance coverage is a very powerful for beneficiaries to obtain well timed and suitable reimbursements. A transparent and environment friendly procedure minimizes tension and guarantees the coverage’s meant advantages are out there. Efficient customer support performs an important function in addressing considerations, resolving problems, and offering fortify right through the claims adventure.The claims procedure for Aetna long-term care insurance coverage is designed to be simple and environment friendly, but it calls for cautious consideration to element.
Figuring out the stairs concerned and the to be had customer support choices is important for a clean enjoy.
Claims Procedure Evaluation
Aetna’s long-term care insurance coverage claims procedure usually follows a standardized process. The method is designed to verify correct analysis of claims and well timed processing. This usually comes to filing required documentation, receiving affirmation of receipt, and anticipating a choice of the declare.
Steps in Submitting a Declare
- Declare Initiation: The declare procedure starts with the insured or their consultant beginning the declare via accumulating the important documentation, which might come with scientific data, care facility invoices, and supporting proof. This preliminary step guarantees all crucial knowledge is compiled.
- Documentation Submission: The compiled documentation is then submitted to Aetna throughout the designated channels. This is able to contain on-line portals, mail, or telephone. A affirmation of receipt is usually issued via Aetna to recognize the declare’s submission.
- Overview and Analysis: Aetna’s claims division critiques the submitted documentation to evaluate the declare’s eligibility and compliance with coverage phrases. This comes to verifying the lined services and products, care facility {qualifications}, and different pertinent components.
- Declare Choice: Aetna problems a choice at the declare, which may also be approval, denial, or request for additional info. The notification features a detailed rationalization of the verdict, referencing explicit coverage provisions or scientific necessities.
- Fee (if authorized): Upon approval, Aetna processes the fee in keeping with the coverage’s phrases and stipulations. The fee approach and timing will probably be communicated obviously.
Buyer Provider Channels
Aetna supplies quite a lot of avenues for purchasers to get admission to customer support fortify referring to claims and policy-related issues.
- On-line Portal: Aetna’s web page incessantly includes a protected on-line portal for gaining access to account knowledge, filing claims, and checking declare standing. This portal supplies self-service features, permitting shoppers to regulate their accounts and claims with no need to touch customer support representatives.
- Telephone Make stronger: A devoted telephone line supplies direct get admission to to customer support representatives. Those representatives can help with claims, solution questions, and supply steerage right through the method. Explicit hours of operation and wait instances will have to be verified at the Aetna web page.
- E mail Make stronger: Piece of email could be a viable choice for explicit inquiries or requests. Aetna will have devoted e-mail addresses for claims-related problems. This comes in handy for filing documentation or for extra advanced queries that require detailed responses.
- Chat Make stronger: Some insurance coverage suppliers be offering reside chat fortify for instant help with explicit questions or problems. This selection is also to be had all through explicit hours or for restricted functions. Test the supply of this provider on Aetna’s web page.
Conventional Declare Processing Time frame
The time-frame for processing a declare varies relying at the complexity of the declare and the quantity of claims being processed. Elements just like the completeness of submitted documentation, the particular protection main points throughout the coverage, and any important follow-up movements can affect the processing time. Aetna in most cases publishes estimated processing instances on their web page.
Illustrative Declare Flowchart
[A flowchart would be visually represented here. It would depict the steps in a claim, including initiation, documentation submission, review, decision, payment (if approved), and potential appeals. Each step would have a clear description and connection to the subsequent step.]
Continuously Requested Questions (FAQ)
This segment addresses commonplace inquiries referring to Aetna long-term care insurance coverage, offering readability on protection specifics, eligibility, and possible boundaries. Figuring out those steadily requested questions can lend a hand folks make told selections about their long-term care insurance coverage wishes.Aetna long-term care insurance coverage insurance policies, like different insurance coverage merchandise, have explicit phrases and stipulations that can impact protection. It is a very powerful to scrupulously evaluation those main points to verify alignment with private wishes and instances.
Protection Limits
Policyholders will have to take note of the utmost receive advantages quantities payable underneath their long-term care insurance coverage insurance policies. Those limits outline the whole monetary repayment the coverage will supply. Figuring out those limits is important to making plans for possible long-term care bills. Insurance policies incessantly specify day by day or per month receive advantages quantities, with the whole payout restricted via the coverage’s most protection.
As an example, a coverage would possibly pay a most of $200 according to day for knowledgeable nursing care, capping general advantages at $730,000 over a five-year duration. This detailed figuring out of utmost protection permits folks to realistically assess the coverage’s monetary capability to handle their care wishes.
Portability
Insurance coverage portability, within the context of long-term care, refers back to the skill to switch protection from one employer or plan to any other. That is a very powerful issue for many who alternate jobs or retire. Insurance policies usually specify the prerequisites underneath which protection may also be transferred. Aetna insurance policies incessantly have explicit portability necessities, together with ready classes or keeping up a definite stage of premiums.
As an example, a coverage would possibly require a continual top class fee historical past for a time period to take care of portability after employment adjustments.
Portability Necessities
Figuring out the necessities for portability is very important to take care of protection in lifestyles transitions. The foundations surrounding shifting protection range from one coverage to any other, and explicit prerequisites will have to be totally reviewed. Usually, those necessities might contain keeping up steady protection, assembly top class fee points in time, and adhering to the coverage’s conditions referring to protection transfers. As an example, a coverage would possibly stipulate {that a} switch can handiest happen inside of a specified time period after a metamorphosis in employment or retirement.
Failure to fulfill those necessities would possibly result in coverage termination or boundaries on advantages.
Protection Denials
Insurance coverage corporations, together with Aetna, reserve the appropriate to disclaim protection in positive scenarios. Figuring out those scenarios is important for policyholders to await possible protection boundaries. Aetna might deny protection if the insured has pre-existing prerequisites, specifically if those prerequisites are associated with long-term care wishes. Moreover, insurance policies might come with exclusions for explicit prerequisites or scenarios, which might lead to protection denials.
Claims may also be denied because of non-compliance with coverage phrases, corresponding to past due top class bills or failure to document adjustments in well being standing.
Continuously Requested Questions and Solutions
- What are the everyday protection limits for long-term care insurance coverage insurance policies? Insurance policies specify most day by day or per month receive advantages quantities, and the whole payout is capped. The precise limits rely at the explicit coverage.
- How does portability paintings with Aetna long-term care insurance coverage? Portability laws Artikel prerequisites for shifting protection, corresponding to keeping up steady protection and assembly top class fee points in time. Coverage phrases will have to be moderately reviewed for switch main points.
- What are the necessities for keeping up portability? Explicit insurance policies require adherence to conditions referring to protection transfers, together with steady protection, top class bills, and well timed reporting of well being standing adjustments.
- What scenarios would possibly lead to protection denial? Protection denials can happen because of pre-existing prerequisites, coverage exclusions, non-compliance with coverage phrases, or failure to document vital well being adjustments.
Illustrations and Visualizations
Figuring out the price and possible prices of long-term care insurance coverage calls for making an allowance for real-world eventualities and fiscal implications. This segment supplies illustrative examples to lend a hand policyholders visualize how the protection would possibly paintings in numerous scenarios and the prospective affect on premiums.Illustrative eventualities and price breakdowns lend a hand possible policyholders evaluation the prospective advantages of long-term care insurance coverage. This permits them to make told selections about protection and top class prices, aligning their insurance coverage wishes with their monetary sources.
Illustrative Policyholder Situation
A 65-year-old, John Smith, anticipates desiring long-term care services and products sooner or later. He’s lately wholesome however understands the prospective dangers related to getting old. He has a reasonable source of revenue and is anxious concerning the monetary burden of possible care wishes. He chooses a plan that covers assisted residing amenities and professional nursing care. This situation illustrates how the coverage can give monetary coverage in such instances.
Conventional Prices of Lengthy-Time period Care Products and services
The price of long-term care services and products varies considerably relying at the stage of care required and the site. Assisted residing amenities usually vary from $3,000 to $10,000 per thirty days, whilst professional nursing amenities can price upwards of $8,000 to $15,000 per thirty days. House well being aides, a much less in depth type of care, usually vary from $20 to $50 according to hour.
Those prices can briefly collect and grow to be a vital monetary burden with out good enough insurance coverage coverage.
Affect of Protection Quantities on Premiums
The volume of protection selected immediately impacts the top class price. The next protection quantity usually leads to the next top class. As an example, a coverage with a day by day good thing about $200 for knowledgeable nursing care will most probably have a decrease top class than a coverage with a day by day good thing about $500. The precise top class depends upon a number of components, together with the policyholder’s age, well being, and selected advantages.
Insurance coverage corporations use actuarial fashions to estimate the possibility of claims and calculate premiums accordingly.
Sorts of Lengthy-Time period Care Amenities Coated
Aetna long-term care insurance coverage usually duvet a spread of amenities, together with:
- Assisted Residing Amenities: Those amenities supply fortify for day by day residing actions, corresponding to bathing, dressing, and meal preparation, for many who need help however don’t require professional nursing care.
- Professional Nursing Amenities: Those amenities supply 24-hour scientific take care of folks requiring extra in depth scientific supervision and professional nursing services and products. This comprises rehabilitation and remedy.
- House Well being Care: House well being care supplies services and products in the house, corresponding to nursing care, bodily remedy, and occupational remedy. This sort of care is incessantly appropriate for many who require fortify however favor to stay in their very own properties.
- Grownup Day Care Facilities: Those facilities supply supervision and actions for many who require help all through the day however can stay of their properties in a single day.
Those other ranges of care mirror the various wishes of policyholders, permitting flexibility in protection choices.
Detailed Representation of Protection, Aetna longer term care insurance coverage
Believe John Smith’s state of affairs. His selected coverage supplies a day by day good thing about $200 for knowledgeable nursing care. If he had been to go into a talented nursing facility for 365 days, the whole receive advantages payable underneath his coverage can be $72,000 (calculated as $200/day
- three hundred and sixty five days/12 months
- 2 years). This quantity is helping offset the really extensive prices of long-term care.
“This protection quantity could be a a very powerful consider assuaging the monetary burden related to long-term care services and products.”
The coverage additionally covers assisted residing and residential well being care, offering additional monetary coverage. The precise top class price for John’s coverage depends upon particular person components, together with age, well being standing, and the particular advantages selected. This illustrative instance supplies a transparent image of ways protection quantities translate into possible monetary coverage.
Concluding Remarks
In conclusion, Aetna long-term care insurance coverage provides treasured coverage for long run care wishes. By means of figuring out the quite a lot of plans, prices, and eligibility standards, you’ll make a well-informed resolution. Have in mind to completely evaluate plans and believe your individual instances prior to creating a dedication.
FAQs
What are the everyday premiums for Aetna long-term care insurance coverage?
Premiums range considerably in accordance with components like age, well being standing, and the selected protection stage. Aetna supplies detailed price knowledge on their web page and in plan paperwork.
How lengthy does it take to procedure a declare?
Declare processing instances rely at the explicit plan and the complexity of the declare. Aetna usually goals for well timed processing, and detailed details about declare timelines is to be had within the coverage paperwork.
What are the average exclusions or boundaries within the protection?
Exclusions and boundaries range via plan. Not unusual exclusions would possibly come with pre-existing prerequisites, positive forms of care no longer assembly explicit standards, or boundaries at the period of protection. At all times discuss with the particular coverage paperwork for actual main points.
Are there any particular provisions for people with pre-existing prerequisites?
Eligibility for long-term care insurance coverage can now and again be impacted via pre-existing prerequisites. Aetna’s insurance policies will have explicit conditions referring to pre-existing prerequisites, so reviewing the coverage paperwork totally is a very powerful.