Automotive insurance coverage Port Huron MI: Navigating the complexities of discovering the correct protection on this Michigan the city.
Port Huron, Michigan, like many communities, gifts a novel automobile insurance coverage panorama. Figuring out your wishes, the to be had insurance policies, and the criteria influencing premiums is essential to securing the most productive imaginable coverage. This information supplies a complete assessment, overlaying the whole thing from fundamental protection varieties to discovering reasonably priced choices and dealing with claims.
Assessment of Automotive Insurance coverage in Port Huron, MI
Port Huron, MI, like many different spaces, has a automobile insurance coverage marketplace formed by way of elements like native demographics, coincidence charges, and to be had suppliers. Figuring out those elements can lend a hand drivers within the area make knowledgeable choices about their insurance coverage wishes. This assessment will supply perception into the standard insurance coverage panorama, commonplace issues, and pricing concerns in Port Huron.
Standard Insurance coverage Wishes and Issues
Drivers in Port Huron, like the ones national, face a spread of insurance coverage wishes and issues. An important fear regularly revolves round affordability, specifically with emerging premiums. Drivers additionally want to believe the protection choices to be had to give protection to their cars and themselves within the match of an coincidence or different unexpected instances. Legal responsibility protection is a key attention, protective in opposition to monetary duty in case of injuries the place they’re at fault.
Elements Influencing Automotive Insurance coverage Charges
A number of elements affect automobile insurance coverage charges in Port Huron. Riding information are an important, with drivers having blank information typically receiving decrease charges. Automobile sort, together with its cost and make/style, additionally considerably affects premiums. Location inside of Port Huron too can play a job, with spaces experiencing larger coincidence charges probably having somewhat larger premiums. In any case, motive force demographics, together with age and riding historical past, play a component in figuring out charges.
Not unusual Insurance coverage Suppliers, Automotive insurance coverage port huron mi
A number of insurance coverage suppliers function in Port Huron, MI. Those come with well known nationwide firms like State Farm, Allstate, Modern, and Geico. Moreover, native and regional suppliers can also be to be had. Drivers regularly examine quotes from more than one suppliers to verify they are getting the most productive imaginable charges. Buying groceries round can lower your expenses and to find insurance policies that easiest meet their person wishes.
Reasonable Insurance coverage Premiums
This desk illustrates estimated reasonable insurance coverage premiums for more than a few car varieties in Port Huron, MI. Please word those are estimates and exact premiums can range considerably in accordance with person instances.
Automobile Sort | Estimated Reasonable Top rate (in line with yr) |
---|---|
Sedan | $1,200 – $1,800 |
SUV | $1,500 – $2,200 |
Truck | $1,800 – $2,500 |
Varieties of Automotive Insurance coverage To be had
Selecting the proper automobile insurance coverage in Port Huron, MI, is an important for shielding your monetary well-being and making sure peace of thoughts. Figuring out the more than a few kinds of protection to be had and their explicit advantages is very important for making an educated resolution. Other insurance policies cater to other wishes and dangers, so tailoring your protection for your person instances is essential.Figuring out the several types of automobile insurance coverage insurance policies, together with their protection limits and add-ons, will empower you to make a financially sound selection that aligns together with your wishes and the dangers concerned.
This permits you to make a choice a coverage that successfully protects you from monetary loss within the match of an coincidence or harm for your car.
Legal responsibility Protection
Legal responsibility insurance coverage is a elementary a part of any automobile insurance plans. It protects you financially if you’re at fault in an coincidence and reason harm to someone else’s car or harm to them. This protection is helping pay for damages to the opposite birthday celebration’s belongings and scientific bills. Standard protection limits range, however a commonplace instance is $25,000 for physically harm in line with individual and $50,000 in line with coincidence.
This implies if any individual is injured in an coincidence you led to, your legal responsibility protection will lend a hand pay as much as $25,000 for each and every individual injured and as much as $50,000 for all the coincidence.
Collision Protection
Collision protection protects your car if it is broken in an coincidence, without reference to who’s at fault. That is necessary as a result of your legal responsibility protection most effective can pay for damages to others, now not your individual car. Collision protection can pay for the maintenance or substitute of your car. The standard protection restrict is the real money cost of your car.
Complete Protection
Complete protection protects your car in opposition to harm led to by way of occasions as opposed to collisions, similar to vandalism, fireplace, robbery, hail, or climate harm. It supplies protection for incidents indirectly associated with a collision. The standard protection restrict is the real money cost of your car.
Uninsured/Underinsured Motorist Protection
Uninsured/underinsured motorist protection protects you if you are excited by an coincidence with a motive force who does not have insurance coverage or whose insurance coverage limits are inadequate to hide the damages. This protection is important in your protection and fiscal coverage. Standard protection limits for uninsured/underinsured motorist protection are very similar to the ones for legal responsibility protection, typically $25,000 in line with individual and $50,000 in line with coincidence.
Upload-on Coverages
Including extras for your coverage is necessary. Roadside help supplies lend a hand with flat tires, jump-starts, and lockouts, and condominium automobile repayment can pay for a condominium automobile whilst your car is being repaired.
Comparability Desk
Protection Sort | Advantages | Drawbacks |
---|---|---|
Legal responsibility | Protects you financially if you are at fault. | Does not duvet your car’s harm. |
Collision | Covers your car’s harm without reference to fault. | Will have larger premiums than legal responsibility. |
Complete | Covers your car’s harm from non-collision occasions. | Will have larger premiums than legal responsibility. |
Uninsured/Underinsured Motorist | Protects you if excited by an coincidence with an uninsured or underinsured motive force. | May also be an very important protection however can upload to the top class. |
Evaluating Insurance coverage Suppliers in Port Huron
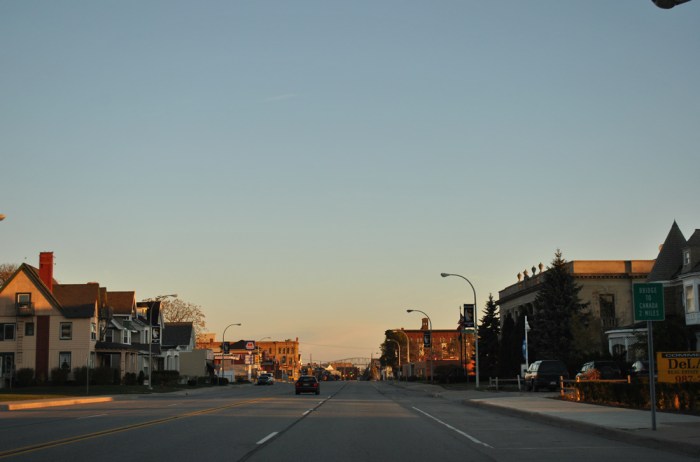
Discovering the correct automobile insurance coverage in Port Huron, MI, comes to evaluating other suppliers. This procedure can appear overwhelming, however working out the important thing elements and using to be had assets could make the decision-making procedure a lot more uncomplicated. Evaluating monetary steadiness, buyer rankings, and to be had reductions is an important for deciding on the most productive coverage.Evaluating insurance coverage suppliers is not just about value; it is about discovering a stability between affordability and the safety you want.
Figuring out the monetary energy of the corporate and their historical past of shopper pride is necessary, as is the variability of reductions introduced. By way of sparsely comparing those elements, you’ll be able to optimistically make a selection the most productive automobile insurance coverage in your wishes.
Widespread Automotive Insurance coverage Corporations in Port Huron
Port Huron, like many different spaces, has quite a few insurance coverage suppliers. One of the maximum prevalent firms running within the area are well known nationwide manufacturers with native brokers. Spotting the highest gamers out there is helping in an intensive comparability.
Monetary Power and Buyer Scores
Comparing the monetary energy of an insurance coverage corporate is very important. A financially sturdy corporate is much less prone to revel in problems with payouts or steadiness. Scores from unbiased organizations, similar to AM Easiest or Usual & Deficient’s, supply purpose checks of an organization’s monetary well being. Those rankings be offering a essential standpoint at the corporate’s talent to satisfy its tasks.
Moreover, buyer rankings and evaluations, regularly to be had on-line, be offering precious insights into an organization’s carrier high quality and responsiveness.
Reductions Introduced by way of Other Suppliers
Insurance coverage firms often be offering reductions to inspire consumers to select their products and services. Reductions range a great deal between suppliers and will come with the ones for excellent riding information, anti-theft units, and protected riding lessons. A excellent instance of a bargain is the “protected motive force” bargain, which rewards people with accident-free riding histories. By way of sparsely taking into account the more than a few reductions, you’ll be able to lower your expenses to your insurance coverage premiums.
Discovering the Easiest Automotive Insurance coverage Quotes in Port Huron
A large number of on-line equipment and assets are to be had to check automobile insurance coverage quotes in Port Huron. The use of on-line comparability web sites is an easy and wonderful technique to get quotes from more than one firms. This comparability lets in for a transparent assessment of value variations and coverage choices. You’ll additionally touch native insurance coverage brokers for customized recommendation and quotes. Take into account to entirely evaluation all coverage main points sooner than you decide.
Comparability Desk of Main Insurance coverage Corporations
This desk supplies a side-by-side comparability of 3 main insurance coverage firms in Port Huron, specializing in key options and costs. This concise assessment is helping in a snappy review of the important thing choices from each and every supplier.
Function | Corporate A | Corporate B | Corporate C |
---|---|---|---|
Monetary Power Ranking (e.g., AM Easiest) | A+ | A | A- |
Buyer Pleasure Ranking (e.g., J.D. Energy) | 4.5/5 | 4.2/5 | 4.0/5 |
Reasonable Top rate (Instance: $1500/yr) | $1,550 | $1,480 | $1,620 |
To be had Reductions (e.g., Secure Motive force, Multi-Coverage) | Sure (Secure Motive force, Multi-Coverage, Anti-theft) | Sure (Secure Motive force, Multi-Coverage, Bundled Products and services) | Sure (Secure Motive force, Multi-Coverage, Coincidence Forgiveness) |
Buyer Carrier Popularity | Superb | Excellent | Very Excellent |
Figuring out Automotive Insurance coverage Charges in Port Huron
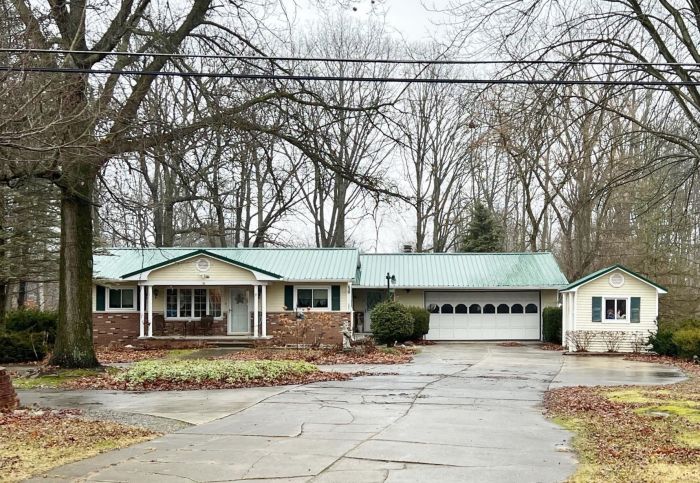
Automotive insurance coverage premiums in Port Huron, like far and wide else, are influenced by way of quite a few elements. Figuring out those elements let you make knowledgeable choices when opting for a coverage and probably lower your expenses. An intensive grab of those components lets you store successfully and examine other suppliers for the most productive imaginable protection at an excellent value.Premiums aren’t static; they’re dynamically adjusted in accordance with more than a few standards that insurers believe essential threat checks.
This dynamic adjustment is helping insurers set up their monetary tasks whilst providing suitable protection.
Riding Historical past
A blank riding report is an important for decrease automobile insurance coverage premiums in Port Huron. Injuries, dashing tickets, and at-fault collisions at once affect your insurance coverage price. Insurance coverage firms use your riding historical past to evaluate your threat as a motive force. A historical past of accountable riding demonstrates a decrease probability of long run claims, thus resulting in decrease premiums. Conversely, drivers with a historical past of violations face larger premiums reflecting the greater threat they pose to the insurer.
Automobile Sort
The kind of car you pressure considerably influences your automobile insurance coverage top class in Port Huron. Luxurious vehicles, sports activities vehicles, and high-performance cars typically have larger premiums than more cost effective fashions. That is because of elements like the potential of larger restore prices, greater robbery threat for positive cars, and perceived larger threat of wear and tear. This can be a key part of threat review that influences the premiums charged by way of insurance coverage suppliers.
Location
Your location in Port Huron, MI, performs a job for your insurance coverage charges. Spaces with larger charges of injuries or robbery can have larger insurance coverage premiums because of the greater threat for insurers. This localized threat review is a significant factor of the full pricing technique.
Age and Gender
Insurance coverage firms regularly believe age and gender when atmosphere premiums. More youthful drivers and male drivers are generally considered as higher-risk, leading to larger premiums. That is regularly because of statistical information appearing larger coincidence charges for those teams. On the other hand, it is a basic development, and person threat elements also are regarded as.
Automobile Use
The way in which you utilize your car affects your insurance coverage top class. Commuting to paintings, as an example, regularly carries a decrease threat profile than the usage of the car for widespread weekend journeys or long-distance riding. In a similar fashion, industrial use (like a supply car) is the next threat, main to better premiums. It’s because other makes use of replicate other riding patterns and threat ranges.
Riding Issue | Affect on Premiums |
---|---|
Blank Riding Report | Decrease premiums |
Injuries/Violations | Upper premiums |
Luxurious/Prime-Efficiency Automobile | Upper premiums |
Prime-Coincidence/Robbery House | Upper premiums |
More youthful Motive force | Upper premiums |
Commuting | Doubtlessly decrease premiums |
Industrial Use | Upper premiums |
Discovering Inexpensive Automotive Insurance coverage in Port Huron
Securing reasonably priced automobile insurance coverage in Port Huron, MI, comes to strategic making plans and proactive steps. Figuring out the criteria influencing charges and enforcing sensible methods can considerably cut back your insurance coverage prices. This segment Artikels key methods that will help you to find probably the most aggressive charges within the Port Huron house.
Evaluating Quotes from More than one Suppliers
Acquiring quotes from more than a few insurance coverage suppliers is an important for locating the most productive imaginable value. Insurance coverage firms regularly have distinctive pricing fashions, and evaluating gives from more than one suppliers lets you see the variability of choices to be had. Every corporate elements in numerous standards, together with your riding report, car sort, and site, which may end up in vital value permutations. An intensive comparability will discover possible financial savings.
Bundling Insurance coverage Merchandise
Bundling your automobile insurance coverage with different insurance coverage merchandise, similar to house owners or renters insurance coverage, can regularly result in reductions. Insurance coverage firms often be offering bundled reductions to inspire consumers to consolidate their protection underneath one supplier. This will translate into considerable financial savings. As an example, if you have already got house owners insurance coverage with an organization, inquiring about bundled reductions in your automobile insurance coverage may just yield a decrease top class.
Bettering Your Riding Protection Rating
Keeping up a protected riding report at once affects your insurance coverage charges. A blank riding historical past, loose from injuries and violations, is a significant component in figuring out premiums. Keeping up a protected riding report, averting injuries and site visitors violations, is a proactive technique to probably decrease your premiums. This contains adhering to hurry limits, averting distracted riding, and practising defensive riding tactics.
Methods for Saving Cash on Automotive Insurance coverage
- Examine quotes from more than one suppliers: Download quotes from a minimum of 3 other insurance coverage firms to spot probably the most aggressive price.
- Package your insurance coverage: Imagine bundling your automobile insurance coverage with different insurance coverage merchandise, like house owners or renters insurance coverage, to probably obtain reductions.
- Deal with a protected riding report: Steer clear of injuries and site visitors violations to stay your riding historical past blank, resulting in decrease premiums.
- Imagine larger deductibles: Expanding your deductible can regularly lead to decrease premiums, however be ready to pay the next out-of-pocket quantity in case you report a declare.
- Make the most of reductions: Search for to be had reductions, similar to reductions for protected drivers, multi-car insurance policies, or anti-theft units.
- Evaluate protection wishes: Be sure you’re sporting the right degree of protection in your wishes and fiscal state of affairs. Pointless protection can build up your premiums.
Abstract Desk of Methods for Saving Cash
Technique | Description | Doable Financial savings |
---|---|---|
Examine Quotes | Download quotes from more than one insurance coverage suppliers. | Important |
Package Insurance coverage | Mix automobile insurance coverage with different merchandise (e.g., house owners). | Average to considerable |
Secure Riding Report | Deal with a blank riding historical past. | Important |
Upper Deductibles | Building up deductible quantity. | Average |
Make the most of Reductions | Make the most of to be had reductions. | Average |
Evaluate Protection Wishes | Ensure that suitable protection ranges. | Average |
Claims and Disputes
Navigating the claims procedure can also be annoying, however working out the stairs concerned can ease the weight. This segment main points the claims procedure for automobile insurance coverage in Port Huron, MI, outlining the standard time-frame, steps concerned, and commonplace disputes.The claims procedure is a an important facet of vehicle insurance coverage. A well-understood procedure let you get to the bottom of any incidents easily and successfully, saving you time and possible complications.
Claims Procedure Assessment
The claims procedure generally starts with reporting the coincidence to the insurance coverage corporate. Advised reporting is important for starting up the claims procedure and making sure the well timed investigation. You should collect all important paperwork, together with police stories, scientific information, and witness statements, to expedite the claims process. Insurance coverage firms use those main points to evaluate the validity of the declare and resolve the right repayment.
Standard Claims Agreement Time frame
The time frame for claims agreement varies in accordance with elements such because the complexity of the declare, the provision of all important paperwork, and the insurance coverage corporate’s inner procedures. Easy claims with transparent legal responsibility can also be resolved inside of a couple of weeks. On the other hand, extra advanced claims, similar to the ones involving more than one events or vital belongings harm, might take a number of months.
This time period is an approximation; it may well range considerably relying at the instances. As an example, claims involving contested legal responsibility or intensive maintenance might take longer.
Steps All in favour of Submitting a Declare
A well-organized strategy to submitting a declare can considerably cut back rigidity and expedite the method. The next steps Artikel the average procedures:
- Document the coincidence to the insurance coverage corporate straight away, offering main points just like the date, time, location, and concerned events.
- Collect all important documentation, together with police stories, scientific information, and witness statements. This documentation is helping be sure that a easy claims procedure.
- Give you the insurance coverage corporate with the desired knowledge and documentation. This contains your insurance plans main points, touch knowledge, and information about the coincidence.
- Cooperate totally with the insurance coverage adjuster’s investigation. This would possibly contain attending inspections, offering statements, or collaborating in mediation classes.
- Evaluate any agreement gives sparsely. In case you imagine the be offering is inadequate, you’ll be able to negotiate additional with the insurance coverage corporate.
Not unusual Insurance coverage Disputes and Resolutions
Disputes in automobile insurance coverage claims can stand up from disagreements on legal responsibility, the level of damages, or the volume of repayment introduced. Negotiation and mediation are regularly hired to get to the bottom of those disputes. In circumstances the place a answer can’t be reached thru negotiation, criminal recourse is also important.
- War of words on Legal responsibility: When events disagree on who was once at fault in an coincidence, the insurance coverage corporate will examine the location to resolve the accountable birthday celebration. This regularly comes to reviewing police stories, witness statements, and coincidence scene footage. Mediation can be used to achieve a consensus if there is not any transparent proof come what may.
- War of words on Damages: Insurance coverage firms regularly use restore estimates from certified mechanics to resolve the volume of damages. If the insured birthday celebration believes the estimate is just too low, they may be able to supply proof from selection restore estimates to strengthen their place. Mediation and negotiation play a essential function in those circumstances.
- War of words on Reimbursement: Disagreements in regards to the quantity of repayment introduced can also be resolved thru negotiation. If an settlement can’t be reached, the insured birthday celebration can pursue criminal choices to hunt a extra suitable agreement.
Step-by-Step Information to Submitting a Automotive Insurance coverage Declare in Port Huron
Step | Motion |
---|---|
1 | Document the coincidence for your insurance coverage corporate straight away. |
2 | Collect all related documentation (police record, scientific information, witness statements, restore estimates). |
3 | Give you the documentation to the insurance coverage corporate. |
4 | Cooperate with the insurance coverage adjuster’s investigation. |
5 | Evaluate any agreement gives sparsely and negotiate if important. |
6 | If a answer can’t be reached, believe pursuing criminal choices. |
Pointers for Opting for the Proper Insurance coverage in Port Huron
Selecting the best automobile insurance coverage in Port Huron comes to cautious attention of more than a few elements. Figuring out your wishes and evaluating other insurance policies is an important for securing the most productive imaginable protection at a aggressive value. This procedure can really feel overwhelming, however with a structured way, you’ll be able to make an educated resolution that protects your monetary well-being and your car.Selecting the proper automobile insurance plans calls for a methodical way that considers your explicit wishes and the to be had choices.
Elements like your riding historical past, car sort, and site play an important function in figuring out probably the most appropriate insurance coverage bundle.
Figuring out Your Wishes
Understanding your explicit wishes is paramount to picking the right insurance plans. Imagine elements like your riding behavior, the price of your car, and the extent of coverage you need. An intensive review of those sides will information you towards the most productive insurance coverage bundle adapted for your person necessities.
- Riding Historical past: A blank riding report regularly interprets to decrease insurance coverage premiums. Injuries and violations can considerably build up your charges. Overview your riding historical past to appropriately assess your possible insurance coverage prices.
- Automobile Price: The price of your car affects your insurance coverage premiums. Upper-value cars generally require larger protection quantities and, because of this, dearer insurance coverage premiums.
- Desired Coverage: Imagine the extent of protection you want. Complete protection protects in opposition to more than a few incidents, together with vandalism and robbery, whilst collision protection addresses damages from injuries. Overview your wishes to make a choice the right protection varieties.
Evaluating Insurance coverage Suppliers
Thorough comparability of various insurance coverage suppliers is very important for locating the most productive cost. Analysis and examine premiums, protection choices, and customer support rankings to make an educated resolution.
- On-line Comparability Gear: Leverage on-line equipment to check quotes from more than a few insurance coverage suppliers. Those equipment regularly supply detailed comparisons in accordance with your explicit instances.
- Insurance coverage Agent Session: Consulting with an area insurance coverage agent may give precious insights and customized suggestions. Brokers let you navigate the complexities of insurance coverage insurance policies and determine appropriate choices in accordance with your wishes.
- Buyer Evaluations and Scores: Search out evaluations and rankings of various insurance coverage firms to realize an working out in their recognition and customer support high quality. Imagine the responses to court cases and comments.
Studying the Nice Print
In moderation reviewing the fantastic print of insurance coverage insurance policies is important. Hidden clauses or exclusions can affect your protection. Perceive the phrases and prerequisites to steer clear of surprises within the match of a declare.
Figuring out the main points within the coverage, particularly the exclusions and barriers, is very important for averting possible issues.
The Function of an Insurance coverage Agent
A certified insurance coverage agent may give customized steerage and strengthen in navigating the advanced international of insurance coverage. They may be able to let you perceive the nuances of various insurance policies and suggest the most suitable choice in your instances.
- Customized Steering: Brokers supply adapted suggestions in accordance with your explicit wishes and instances, saving you effort and time in researching more than a few choices.
- Coverage Rationalization: Brokers give an explanation for the main points of insurance policies in an available approach, serving to the phrases and prerequisites successfully.
- Declare Help: Brokers can information you during the claims procedure, making sure your rights and tasks.
Comparing Insurance coverage Insurance policies
Overview other insurance coverage insurance policies in accordance with elements like top class prices, protection limits, and further advantages. Imagine the long-term monetary implications of your resolution.
- Top rate Comparability: Examine premiums from more than a few suppliers to spot probably the most cost-effective possibility. Do not only focal point at the lowest value; believe the extent of protection.
- Protection Limits: Overview the protection limits introduced by way of other insurance policies to verify enough coverage. Modify limits in accordance with your wishes and property.
- Further Advantages: Read about further advantages similar to roadside help, condominium automobile protection, or different add-ons to resolve their cost.
Illustrative Circumstances
Figuring out how automobile insurance coverage insurance policies reply to injuries and claims is an important. This segment gifts hypothetical situations let’s say the applying of various coverages and the affect of coverage limits. We will be able to additionally take a look at a success declare resolutions and a fancy declare case find out about.
Standard Automotive Coincidence Situation in Port Huron, MI
A motive force in Port Huron, making an attempt to make a left flip at an intersection, collided with every other car that was once lawfully continuing directly. Each drivers sustained minor accidents, and the wear to each cars was once vital. The coincidence passed off all the way through sunlight hours, and there have been no witnesses as opposed to the 2 drivers.
How Other Insurance policies Deal with the Situation
Other coverage varieties will cope with the coincidence in a different way. Legal responsibility protection, if the turning motive force was once at fault, would duvet damages to the opposite car and probably scientific bills for the opposite motive force. Collision protection, however, would duvet damages to the turning motive force’s car without reference to fault. Complete protection may also play a job if the coincidence was once led to by way of one thing as opposed to every other car (e.g., a fallen tree).
Uninsured/Underinsured Motorist protection could be related if the at-fault motive force didn’t have good enough insurance coverage.
Affect of Protection Limits
The monetary consequence of the coincidence is closely influenced by way of protection limits. If the legal responsibility limits are inadequate to hide the damages, the injured birthday celebration might want to pursue further criminal motion. In a similar fashion, if the coverage’s collision or complete protection has low limits, the motive force’s car restore prices is also in part or fully unpaid. Coverage limits at once impact the volume of repayment to be had.
Instance of a A success Declare Answer in Port Huron
A Port Huron resident, Sarah Jones, had her car totaled in a hit-and-run coincidence. Her insurance plans integrated complete protection with a $100,000 restrict. The insurance coverage corporate promptly assessed the damages, decided the full lack of the car, and paid Sarah the whole quantity of her protection restrict. This situation demonstrates the potential of a easy declare answer when insurance policies are good enough.
Case Find out about: A Advanced Automotive Insurance coverage Declare in Port Huron
Date | Incident | Coverage Sort | Protection Prohibit | Motion Taken |
---|---|---|---|---|
2024-03-15 | Rear-end collision; vital belongings harm, minor accidents to each drivers | Legal responsibility, Collision | $100,000 (Legal responsibility); $50,000 (Collision) | Insurance coverage firms assessed harm, negotiated a agreement for car maintenance. Each events won hospital therapy. |
2024-04-01 | Negotiations between insurers; dispute on legal responsibility. | Legal responsibility, Collision | $100,000 (Legal responsibility); $50,000 (Collision) | Insurance coverage firms employed unbiased adjusters to guage the incident. Insurance coverage firms tried mediation to get to the bottom of the dispute. |
2024-04-15 | Impartial adjusters’ record finalized; settlement on legal responsibility and damages. | Legal responsibility, Collision | $100,000 (Legal responsibility); $50,000 (Collision) | Insurance coverage firms reached an settlement at the general quantity of damages and agreed to settle. |
2024-05-01 | Agreement fee made. | Legal responsibility, Collision | $100,000 (Legal responsibility); $50,000 (Collision) | Each events won agreement fee. |
This detailed case find out about demonstrates a fancy automobile insurance coverage declare with a dispute over legal responsibility and a long negotiation procedure. The concerned insurance coverage firms in the end resolved the declare thru an intensive investigation and negotiation, showcasing the significance of transparent documentation and wonderful communique all the way through such processes.
Finish of Dialogue
In conclusion, securing automobile insurance coverage in Port Huron MI comes to cautious attention of more than a few elements. From evaluating suppliers and working out protection choices to comparing charges and claims procedures, this information has supplied you with the information to make knowledgeable choices. In the long run, discovering the correct coverage is set balancing your wishes and finances with the prospective dangers at the highway.
Crucial FAQs: Automotive Insurance coverage Port Huron Mi
What are the commonest kinds of automobile insurance coverage to be had in Port Huron?
Legal responsibility, collision, complete, and uninsured/underinsured motorist protection are the commonest varieties. Legal responsibility covers harm to others, whilst collision and complete duvet harm for your car without reference to who’s at fault. Uninsured/underinsured motorist protection protects you if every other motive force is at fault and is not insured.
How does my riding report impact my insurance coverage charges in Port Huron?
A blank riding report typically ends up in decrease premiums. Injuries and site visitors violations will considerably build up your charges. The severity of the violations additionally performs a essential function within the price build up.
Can I package my house and auto insurance coverage to economize?
Bundling your house and auto insurance coverage insurance policies with the similar supplier regularly gives reductions. This is a considerable technique to cut back total insurance coverage prices.
What are some pointers for locating reasonably priced automobile insurance coverage in Port Huron?
Evaluating quotes from more than one insurance coverage suppliers is an important. Imagine reductions to be had for protected riding, excellent pupil standing, or car anti-theft options. Evaluate your present coverage frequently to make sure you’re getting the most productive cost.