Am i able to insure my girlfriends automotive – Can I insure my female friend’s automotive? This query arises when taking into consideration shared car use and duties. Other insurance coverage insurance policies, elements affecting premiums, and protection choices all play a the most important position in making an educated resolution. This complete comparability will discover quite a lot of facets, from prison implications to sensible steps, making sure you’ve a transparent working out of the method.
Working out the several types of insurance coverage insurance policies to be had, reminiscent of legal responsibility, complete, and collision, is very important. This information supplies an in depth review, permitting you to weigh the price and protection to make the appropriate selection to your explicit scenario.
Insuring a Spouse’s Car

Insuring a spouse’s car comes to a fancy interaction of prison, monetary, and private issues. Working out the quite a lot of aspects of this procedure is the most important for making sure good enough coverage and minimizing possible dangers. This comprises spotting the other insurance coverage sorts to be had and the monetary duties related to every.
Varieties of Insurance coverage Insurance policies Acceptable to a Spouse’s Car
Other insurance coverage insurance policies cater to numerous wishes and cases. A complete working out of those insurance policies is very important for making knowledgeable selections. Legal responsibility protection, collision protection, and complete protection are the most important components. Moreover, working out uninsured/underinsured motorist protection and extra add-ons may be necessary.
- Legal responsibility Protection: This coverage covers damages to folks’s assets or accidents sustained by means of others because of an coincidence involving the car. It’s most often required by means of legislation in maximum jurisdictions.
- Collision Protection: This kind of protection can pay for damages to the insured car without reference to who’s at fault in an coincidence. That is steadily a the most important element in keeping up the car’s price and capability.
- Complete Protection: This coverage covers damages to the insured car from perils as opposed to collision, reminiscent of hearth, robbery, vandalism, or climate occasions. It supplies a security web for unexpected cases.
- Uninsured/Underinsured Motorist Protection: This protection safeguards in opposition to incidents involving drivers missing or possessing inadequate insurance coverage. This protection is important for cover in opposition to possible monetary burdens.
- Further Upload-ons: Insurance policies might come with roadside help, condo automotive repayment, or different supplementary advantages to give a boost to the safety and comfort of proudly owning the car.
Felony and Monetary Implications of Insuring a Spouse’s Car
Felony and fiscal ramifications of insuring a spouse’s car necessitate cautious attention. Figuring out possession and duty is paramount for efficient coverage and suitable protection. Working out the prison implications is essential to make sure the safety of all events concerned. Moreover, monetary implications, reminiscent of top class prices and protection barriers, are integral portions of the method.
- Possession and Accountability: Setting up transparent possession and duty is important for figuring out who’s legally obligated to pay for damages. This readability is very important for resolving claims rather and successfully.
- Monetary Implications: Top class prices can range relying at the car’s make, style, and utilization historical past. Protection barriers also are necessary to know and be sure that they align with the worth of the car and the desires of the events concerned.
- Coverage Boundaries: It is the most important to know the coverage’s barriers to forestall unexpected monetary burdens in case of injuries or injury. Particular exclusions and prerequisites will have to be moderately tested.
Not unusual Eventualities The place Insuring a Spouse’s Car Is Vital or Advisable
Positive scenarios spotlight the need or benefits of insuring a spouse’s car. This proactive method can considerably mitigate possible dangers and offer protection to shared pursuits. As an example, if the spouse is a brand new motive force with restricted enjoy or if the car is a prized ownership, insuring it may be a essential step.
Coverage Sort | Protection | Value Issues |
---|---|---|
Legal responsibility | Covers damages to others’ assets and accidents | Most often decrease premiums in comparison to different sorts; would possibly not quilt injury to insured car |
Collision | Covers injury to the car without reference to fault | Upper premiums than legal responsibility; protects car’s price |
Complete | Covers damages from perils as opposed to collision | Upper premiums than legal responsibility; the most important for safeguarding in opposition to robbery, vandalism, and herbal screw ups |
Uninsured/Underinsured Motorist | Covers damages if the at-fault motive force is uninsured or underinsured | Crucial for complete coverage; premiums range in keeping with possibility elements |
Elements Affecting Insurance coverage Premiums
Insuring a spouse’s car comes to attention of quite a lot of elements impacting top class prices. Working out those elements is the most important for knowledgeable decision-making and making sure suitable protection. Premiums aren’t static; they differ in keeping with a number of variables, making proactive research very important.The price of insuring a spouse’s car is influenced by means of a mess of interconnected elements, from the spouse’s using checklist to the car’s traits.
Those components give a contribution to the total possibility evaluate carried out by means of insurance coverage corporations, at once affecting the top class quantity. Each and every issue, thought to be in isolation or together, can considerably have an effect on the overall value of the coverage.
Riding Historical past
Riding historical past is a number one determinant in insurance coverage top class calculations. A historical past of injuries, visitors violations, or claims considerably raises the top class. Insurance coverage corporations assess possibility in keeping with the frequency and severity of previous incidents. This analysis is the most important, because it at once displays the possibility of long term claims. As an example, a motive force with a historical past of rushing tickets and at-fault injuries will most probably face considerably upper premiums in comparison to a motive force with a blank checklist.
The severity and frequency of incidents are assessed one by one, with extra critical offenses impacting the top class extra closely.
Car Sort
The kind of car considerably impacts insurance coverage premiums. Luxurious automobiles, sports activities vehicles, and high-performance automobiles steadily include upper premiums because of the higher possible for injury and service prices. That is at once related to the price of substitute portions and possible for upper restore expenses. Conversely, less expensive automobiles, particularly the ones with a decrease price, in most cases have decrease premiums.
The perceived possibility of robbery or injury additionally performs a job.
Location
Geographic location is some other key issue influencing insurance coverage premiums. Spaces with upper charges of injuries or robbery enjoy upper premiums. That is steadily a mirrored image of native visitors patterns, coincidence frequency, or the superiority of explicit forms of criminality. Insurance coverage corporations analyze ancient knowledge for a given space to regulate premiums accordingly. As an example, city spaces with excessive visitors congestion might see upper premiums than rural spaces with decrease visitors quantity.
The density of visitors and the precise demographics of the world also are elements.
Car Options and Protection Rankings
Car options and protection scores considerably have an effect on insurance coverage prices. Automobiles supplied with complicated security measures, reminiscent of airbags, anti-lock brakes, and digital steadiness keep watch over, steadily obtain decrease premiums. Those options scale back the danger of injuries and accidents, reducing the prospective value for insurance coverage corporations. Conversely, automobiles with fewer security measures might result in upper premiums because of the perceived upper possibility.
The have an effect on of protection scores on premiums is in most cases demonstrable. As an example, a car with a best protection score from organizations just like the Insurance coverage Institute for Freeway Protection (IIHS) or the Nationwide Freeway Visitors Protection Management (NHTSA) steadily qualifies for decrease premiums.
Have an effect on of Elements on Insurance coverage Prices
Issue | Have an effect on on Top class | Instance |
---|---|---|
Riding Historical past (Injuries, Violations) | Higher | A motive force with more than one injuries or rushing tickets will most probably pay extra. |
Car Sort (Luxurious, Sports activities Automotive) | Higher | Upper-performance automobiles steadily command upper premiums. |
Location (Top-accident space) | Higher | City spaces with upper visitors density most often have upper premiums. |
Car Options (Protection Options) | Reduced | Automobiles with complicated security measures, reminiscent of airbags, most often obtain decrease premiums. |
Protection Choices and Issues
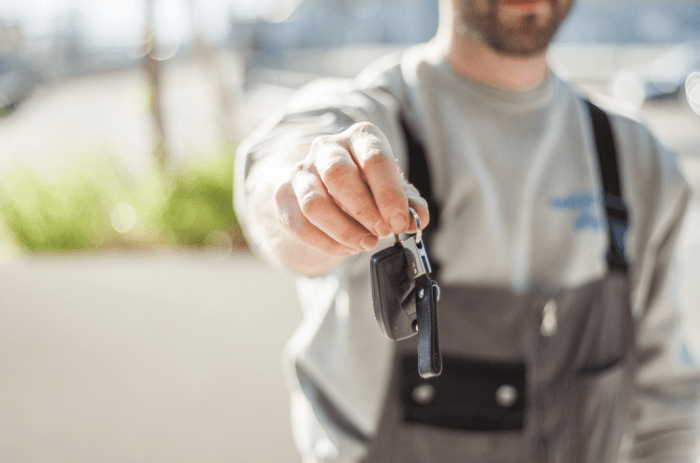
Deciding on suitable protection for a spouse’s car is the most important for monetary coverage and peace of thoughts. Moderately comparing the to be had choices and working out their implications is paramount to creating an educated resolution. An intensive working out of legal responsibility, complete, and collision protection, in addition to supplementary choices like roadside help, empowers accountable car possession.Thorough research of protection choices lets in for the choice of insurance policies that align with person wishes and fiscal cases.
This procedure necessitates a cautious comparability of quite a lot of protection ranges to make sure optimum coverage in opposition to possible dangers and related prices.
Varieties of Protection To be had
Quite a lot of insurance coverage coverages are to be had for a spouse’s car, every designed to handle explicit dangers. Those coverages are adapted to give protection to in opposition to other possible damages and incidents.
- Legal responsibility Insurance coverage: This basic protection is remitted in maximum jurisdictions and protects in opposition to claims coming up from damages inflicted on others. It will be significant for overlaying the monetary duty if an coincidence leads to accidents or assets injury to some other birthday celebration. With out legal responsibility protection, non-public belongings is also in danger.
- Complete Protection: This broadens coverage past injuries to incorporate injury from occasions like vandalism, hearth, robbery, hail, and weather-related incidents. Complete protection supplies an extra layer of safety in opposition to unexpected occasions that would possibly injury the car.
- Collision Protection: This protection addresses injury to the insured car because of a collision with some other object or car. It is very important for repairing or changing the car in case of an coincidence, without reference to who’s at fault.
Significance of Legal responsibility Insurance coverage
Legal responsibility insurance coverage is a cornerstone of car insurance coverage. It safeguards the policyholder’s monetary well-being by means of offering a security web in opposition to claims coming up from injuries. Legal responsibility protection can pay for damages inflicted on others, fighting non-public belongings from being jeopardized. That is steadily legally required and represents the minimal important protection.
Importance of Complete and Collision Protection
Complete and collision protection be offering essential coverage in opposition to dangers past injuries. Complete protection safeguards in opposition to quite a lot of incidents, together with vandalism, hearth, robbery, and herbal screw ups, safeguarding the car’s price. Collision protection, conversely, particularly addresses injury coming up from collisions, whether or not or no longer the insured birthday celebration is at fault. This mixture of coverages supplies complete coverage for the car, without reference to the cases.
Advantages of Further Protection Choices
Past the core coverages, supplementary choices like roadside help may give vital benefits. Roadside help gives help with flat tires, jump-starts, lockouts, and different not unusual vehicle-related problems. This complements comfort and decreases the strain related to surprising car issues.
Comparability of Protection Ranges
Other protection ranges be offering various levels of coverage. The selection depends upon elements such because the car’s price, the motive force’s using checklist, and fiscal capability. As an example, a more moderen, costlier car would possibly necessitate upper ranges of protection to make sure good enough monetary coverage.
Protection Degree | Description | Conventional Value (Estimated) | Advantages |
---|---|---|---|
Fundamental Legal responsibility | Covers damages to others most effective. | $100 – $300/12 months | Minimal prison requirement in maximum jurisdictions. |
Complete and Collision | Covers injury to the insured car without reference to fault. | $200 – $500/12 months | Protects in opposition to quite a lot of dangers past injuries. |
Complete, Collision, and Roadside Help | Provides roadside help for additonal comfort. | $300 – $700/12 months | Supplies help with vehicle-related problems. |
Insurance coverage Corporate and Coverage Variety
Deciding on the best insurance coverage corporate and coverage for a spouse’s car is the most important for monetary coverage and peace of thoughts. Cautious attention of quite a lot of elements, together with protection choices, premiums, and corporate recognition, is very important to make sure good enough coverage whilst minimizing prices. An intensive comparability procedure is essential to attaining the most efficient imaginable end result.
Respected Insurance coverage Firms
A lot of respected insurance coverage corporations be offering insurance policies adapted for spouse’s automobiles. Opting for an organization with a robust monitor checklist and favorable monetary status is paramount. An organization’s historical past of recommended claims dealing with and customer support may be a significant component to imagine.
- Aetna Insurance coverage
- Allstate Insurance coverage
- Farmers Insurance coverage
- Geico
- Liberty Mutual Insurance coverage
- Modern Insurance coverage
- State Farm
Evaluating Insurance coverage Choices
Evaluating the choices of various insurance coverage suppliers is very important for making an educated resolution. Each and every corporate will have distinct protection choices, top class constructions, and customer support protocols. Elements reminiscent of geographic location, car sort, and using historical past will affect top class quantities.
Coverage Comparability Technique
A scientific comparability means is essential for settling on essentially the most appropriate coverage. This comes to comparing protection main points, top class prices, and any further options. A tabular illustration lets in for a transparent and concise review of the other insurance policies.
Corporate | Protection | Top class |
---|---|---|
Geico | Complete, Collision, Legal responsibility | $1200 according to 12 months |
State Farm | Complete, Collision, Legal responsibility, Uninsured/Underinsured Motorist | $1500 according to 12 months |
Modern | Complete, Collision, Legal responsibility, Uninsured/Underinsured Motorist, Roadside Help | $1350 according to 12 months |
Elements to Believe
A number of elements affect the choice of an insurance coverage corporate for a spouse’s car. Those come with monetary steadiness, claims dealing with enjoy, customer support scores, and coverage options. Moreover, the coverage’s phrases and prerequisites, together with exclusions and barriers, will have to be moderately scrutinized.
Coverage Acquisition Procedure
The coverage acquisition procedure comes to a number of key steps. Those come with amassing important documentation, finishing an utility, and reviewing the coverage main points. Thorough working out of the phrases and prerequisites is very important to make sure the coverage aligns with the desires and expectancies of the policyholder.
Acquiring a Coverage for a Spouse’s Car
Acquiring a coverage for a spouse’s car calls for correct authorization and documentation. A transparent working out of the method and required forms guarantees a clean and environment friendly acquisition. The policyholder should supply important documentation, together with the car’s name, evidence of possession, and the spouse’s motive force’s license. The insurance coverage supplier may additionally request more information, such because the car’s make, style, and 12 months.
Felony and Monetary Implications
Insuring a spouse’s car carries prison and fiscal duties that stretch past the easy act of buying protection. Working out those implications is the most important for making sure each events are safe and any possible disputes are minimized. This phase delves into the prison necessities, monetary issues, and possible conflicts related to this kind of insurance coverage.The monetary implications of insuring a spouse’s car lengthen past the top class itself.
Possible claims, coming up from injuries or different lined occasions, can considerably have an effect on each events financially. As it should be assessing those dangers is essential for a valid insurance coverage technique.
Felony Necessities for Insuring a Spouse’s Car
Other jurisdictions have various prison necessities referring to car insurance coverage. Some jurisdictions might mandate that the car proprietor be the only real insured, whilst others might allow joint insurance coverage preparations. Failure to agree to those necessities may end up in prison ramifications. It is very important to discuss with prison pros and insurance coverage suppliers within the related jurisdiction to resolve the proper prison prerequisites.
Consultations with native prison government can ensure that compliance and keep away from possible consequences.
Monetary Implications of Insuring a Spouse’s Car
The monetary implications surround insurance coverage premiums and the opportunity of claims. Premiums range in keeping with a number of elements, together with the car’s make, style, and 12 months, in addition to the motive force’s historical past. In some circumstances, the insured motive force’s historical past is also thought to be as an element within the top class calculation. It is very important to scrupulously assess those elements when comparing the monetary have an effect on.A possible declare, stemming from an coincidence involving the car, could have a considerable monetary have an effect on on each events.
The declare procedure can contain negotiation between the insurance coverage corporations, figuring out legal responsibility, and settling reimbursement. As it should be estimating those possible prices is the most important for monetary making plans. The monetary burden of a declare will also be vital, impacting the monetary steadiness of each events concerned.
Possible Disputes or Conflicts Referring to Insurance coverage Protection
Disputes can rise up referring to legal responsibility in an coincidence involving a spouse’s car. Those disputes might rise up from unclear definitions of possession, utilization rights, or the department of duties. Pre-existing agreements and transparent verbal exchange referring to insurance policy can assist mitigate those conflicts. Defining the precise duties for the car’s upkeep and insurance coverage in a written settlement can save you long term disputes.
Addressing Felony and Monetary Problems
Thorough documentation of the car’s possession, utilization agreements, and insurance coverage preparations is the most important. Those paperwork can be utilized as proof in case of disputes. Open verbal exchange between companions is essential for heading off misunderstandings and clarifying any ambiguities within the settlement. An in depth and legally sound contract can save you disputes at some point. Looking for prison recommend may give steering at the suitable prison framework and make sure the settlement is legally sound.
Structured Evaluate of Felony and Monetary Obligations
Accountability | Description |
---|---|
Possession | Figuring out the prison possession of the car is important. This clarifies who’s answerable for upkeep, upkeep, and insurance coverage. |
Utilization Agreements | Defining who is permitted to pressure the car is essential for organising legal responsibility in case of an coincidence. |
Insurance coverage Protection | Obviously outlining the insurance policy, together with the coverage limits, and the events answerable for bills is important. |
Claims Procedure | A transparent working out of the claims procedure, together with the jobs of each events and the insurance coverage corporations, is very important. |
Monetary Contributions | Setting up the monetary duties for premiums and possible claims can save you disputes. |
Sensible Steps and Procedures
Insuring a spouse’s car necessitates a structured method to make sure a clean and compliant procedure. This comes to cautious attention of documentation, verbal exchange, and record-keeping to mitigate possible problems and take care of a transparent working out of the insurance plans. The next sections Artikel the sensible steps and procedures concerned.
Beginning the Insurance coverage Procedure
The preliminary step comes to amassing the important knowledge and documentation to begin the insurance coverage procedure. Thorough preparation is the most important to expedite the appliance and keep away from delays.
- Car Main points: Correct car id, together with the make, style, 12 months, VIN (Car Id Quantity), and any related adjustments, is paramount. Wrong knowledge may end up in coverage inaccuracies and even denial of protection.
- Policyholder Knowledge: The applicant’s non-public main points, together with complete identify, deal with, date of start, and motive force’s license knowledge, are very important for organising the policyholder’s identification and eligibility.
- Monetary Knowledge: Offering correct monetary main points, reminiscent of fee historical past and credit score ranking, aids the insurance coverage supplier in assessing possibility and figuring out suitable premiums.
- Riding Document: The policyholder’s using checklist, together with any injuries or violations, is a essential issue within the insurance coverage evaluate. Offering a whole and correct checklist is very important.
Acquiring Vital Paperwork
A complete set of paperwork is needed for the insurance coverage utility. Failure to supply entire and correct documentation might result in delays or headaches.
- Evidence of Possession: Legitimate documentation of car possession, such because the name or registration, is indispensable. The record will have to be authentic or a licensed replica.
- Motive force’s Licenses: Unique or qualified copies of the motive force’s licenses of all named drivers at the coverage are required.
- Insurance coverage Knowledge: If the car was once up to now insured, offering the main points of the former coverage, together with the coverage quantity and the insurance coverage corporate, is the most important.
- Evidence of Deal with: Application expenses, financial institution statements, or different authentic paperwork that test the policyholder’s deal with are required.
Conversation with the Insurance coverage Supplier
Open and efficient verbal exchange with the insurance coverage supplier is essential for a clean insurance coverage procedure. Transparent and well timed verbal exchange facilitates a streamlined procedure.
- Coverage Queries: Any questions in regards to the coverage will have to be addressed promptly and as it should be during the designated verbal exchange channels. This comprises telephone calls, emails, or the insurer’s on-line portal.
- Coverage Adjustments: Any adjustments within the car, reminiscent of adjustments or the addition/elimination of named drivers, will have to be communicated promptly to the insurance coverage supplier to make sure the coverage stays correct.
- Claims Reporting: If a declare arises, the declare will have to be reported promptly to the insurance coverage supplier during the designated channels, following the precise procedures Artikeld within the coverage.
Keeping up Information
Keeping up correct information of the insurance plans is the most important for long term reference and possible claims.
- Coverage Paperwork: Retain all coverage paperwork, together with the insurance coverage certificates, declarations web page, and any addendums, in a safe and arranged method.
- Cost Information: Deal with information of all insurance coverage bills made, together with dates, quantities, and fee strategies.
- Correspondence: Make a copy of all correspondence with the insurance coverage supplier, together with emails, letters, and call information, associated with the coverage.
Procedure Glide Chart
The next float chart Artikels the method for insuring a spouse’s car:
Step | Motion |
---|---|
1 | Acquire required paperwork and knowledge. |
2 | Entire the insurance coverage utility shape. |
3 | Put up the appliance and paperwork to the insurance coverage supplier. |
4 | Obtain affirmation of the appliance and coverage main points. |
5 | Pay the top class as according to the coverage phrases. |
6 | Deal with correct information of the coverage and correspondence. |
Possible Issues and Answers
Insuring a spouse’s car can introduce distinctive demanding situations, specifically relating to possible disputes and declare solution. Working out those possible problems and proactive methods for mitigation is the most important for keeping up a harmonious courting and making sure the safety of each events’ pursuits.
Figuring out Possible Issues
Difficulties might rise up in quite a lot of facets of insuring a spouse’s car, starting from differing views on protection ranges to disagreements over declare dealing with. Misunderstandings referring to coverage phrases, duties, and the results of shared use too can result in rivalry. Discrepancies in expectancies referring to insurance coverage premiums and protection sorts can create pressure and possible disputes. Additional complicating issues, adjustments in non-public cases, reminiscent of activity loss or higher using frequency, might necessitate changes to the insurance plans, doubtlessly introducing disagreements concerning the important adjustments.
Possible Disputes Referring to Insurance coverage Claims
Disputes relating to insurance coverage claims steadily stem from differing interpretations of coverage phrases or perceived inequities within the declare procedure. One spouse would possibly really feel that the opposite isn’t adequately adhering to coverage necessities, reminiscent of correct reporting of injuries or keeping up car upkeep information. A loss of transparent verbal exchange or a failure to determine a shared working out of duties in regards to the car’s insurance coverage may end up in disputes.
That is very true when there are differing evaluations at the want for extra protection, reminiscent of roadside help or complete insurance coverage. Unclear or incomplete documentation too can impede the declare procedure, doubtlessly leading to delays and frustration.
Resolving Disputes and Claims
Setting up a transparent and complete verbal exchange plan is essential in resolving disputes or claims associated with a spouse’s car insurance coverage. Open discussion and a dedication to discovering mutually agreeable answers are paramount. Formal documentation, together with copies of the insurance plans, verbal exchange information, and any related proof, can facilitate a smoother declare solution procedure. Looking for prison recommend, if important, may give an function viewpoint and be sure that the rights and pursuits of each events are safe.
Methods for Mitigating Possible Issues
Preemptive measures can considerably scale back the possibility of disputes coming up. Making a shared working out of duties and expectancies surrounding the car’s insurance coverage is the most important. This comprises agreeing upon protection ranges, premiums, and reporting procedures. Setting up a transparent written settlement, together with information about shared utilization and duties, may give a framework for resolving possible disagreements. Common evaluation of the insurance plans and verbal exchange referring to any adjustments to forcing behavior or cases are very important.
Not unusual Problems and Answers
Factor | Motive | Answer |
---|---|---|
Confrontation on protection ranges | Differing priorities referring to insurance coverage sorts and protection limits | Identify a written settlement outlining explicit protection wishes, negotiate mutually appropriate ranges, and evaluation the coverage often. |
Discrepancies in declare dealing with | Differing interpretations of coverage phrases or failure to file incidents promptly. | Deal with transparent verbal exchange, record all related knowledge, and seek the advice of prison recommend if important. |
Unclear duties for upkeep and utilization | Loss of outlined roles relating to car maintenance and using | Identify a written settlement detailing duties for car upkeep, utilization, and reporting incidents. |
Illustrative Eventualities: Can I Insure My Girlfriends Automotive
Insuring a spouse’s car gifts a fancy interaction of monetary and prison issues. Cautious analysis of quite a lot of eventualities is the most important for making knowledgeable selections referring to protection and coverage. Elements reminiscent of person monetary scenarios, using information, and the precise cases surrounding the car’s use considerably have an effect on the total suitability of insurance coverage.
Situation of Mutual Get advantages
A pair collectively owns a car and each often put it to use for commuting to paintings and shared errands. Each and every person’s insurance coverage insurance policies would possibly not adequately quilt the car in case of an coincidence involving the opposite motive force or vital damages to the car. Insuring the car underneath one coverage supplies complete protection for each events. This situation demonstrates a mutual receive advantages, mitigating the monetary burden will have to an coincidence happen.
By means of combining insurance coverage insurance policies, the couple can doubtlessly decrease their premiums and take care of complete protection.
Situation of Useless Expenditure
A spouse contributes financially to a family, however hardly makes use of a car for private causes. On this situation, insuring the car underneath the spouse’s identify is probably not financially prudent. If the opposite spouse is the principle motive force, and the car is most commonly used for his or her functions, then the present insurance policy might already adequately deal with possible damages.
This example demonstrates a situation the place insuring the car underneath the spouse’s identify can be an pointless expense.
Illustrative Injury Protection
Believe a scenario the place a spouse’s car is curious about an coincidence leading to vital injury. The insurance plans would quilt restore prices or, if deemed a complete loss, supply a payout in keeping with the car’s appraised price. The insurance policy is determined by the coverage’s phrases and the precise cases of the coincidence. This situation highlights the direct monetary coverage insurance coverage gives.
Coverage for Each Events, Am i able to insure my girlfriends automotive
Insurance plans extends to each events, making sure that each companions are safe financially in case of damages. If one spouse is at fault, the coverage would quilt the opposite spouse’s damages as much as the coverage limits. This reciprocal coverage strengthens the bond of shared duty and fiscal safety. The insurance coverage corporate’s claims procedure would apply established procedures to resolve legal responsibility and payout quantities.
When Insurance coverage is Inadequate
In circumstances of serious injury or injuries involving negligence, insurance policy would possibly not absolutely atone for the losses. This is able to contain a situation the place the opposite birthday celebration concerned within the coincidence is uninsured or underinsured, resulting in a shortfall in reimbursement. Further prison recourse, reminiscent of submitting a non-public harm lawsuit, may well be important to handle the shortfall.
The constraints of insurance policy should be known to hunt suitable prison avenues for reimbursement.
Ultimate Ideas
In conclusion, insuring a spouse’s car comes to cautious attention of quite a lot of elements. Working out the coverage sorts, protection choices, and value implications is secret to meaking the appropriate resolution. This comparability gives treasured insights into navigating the complexities of insuring a shared car, enabling you to make an educated and financially sound selection.
FAQ Information
Can I upload my female friend’s automotive to my current coverage?
Probably, however it depends upon your present coverage and the insurance coverage supplier. It’s possible you’ll wish to upload the car and doubtlessly regulate your top class. Touch your insurer for explicit main points.
What if my female friend is the principle motive force?
Her using historical past and any previous injuries will considerably have an effect on the top class. This data should be supplied to the insurance coverage corporate to resolve the overall value.
Does insurance coverage quilt damages if the automobile is stolen?
Complete protection steadily comprises robbery coverage. Then again, take a look at the specifics of your coverage for main points at the extent of protection.
What paperwork are had to insure a spouse’s car?
You can most often want the car’s registration, evidence of possession, and your spouse’s using historical past. Touch your insurance coverage supplier for the precise checklist of required paperwork.